When Designing Castings, Don’t Get Shut-Out by Shut-Offs…and Other Pitfalls to Avoid.
Castings are considered highly engineered components that bring value to the end customer. They are an economical way of solving difficult design related engineering challenges. While casting technology has evolved over the years to deliver more capabilities to the foundryman, there are limitations of what can be done, both physically and cost effectively.
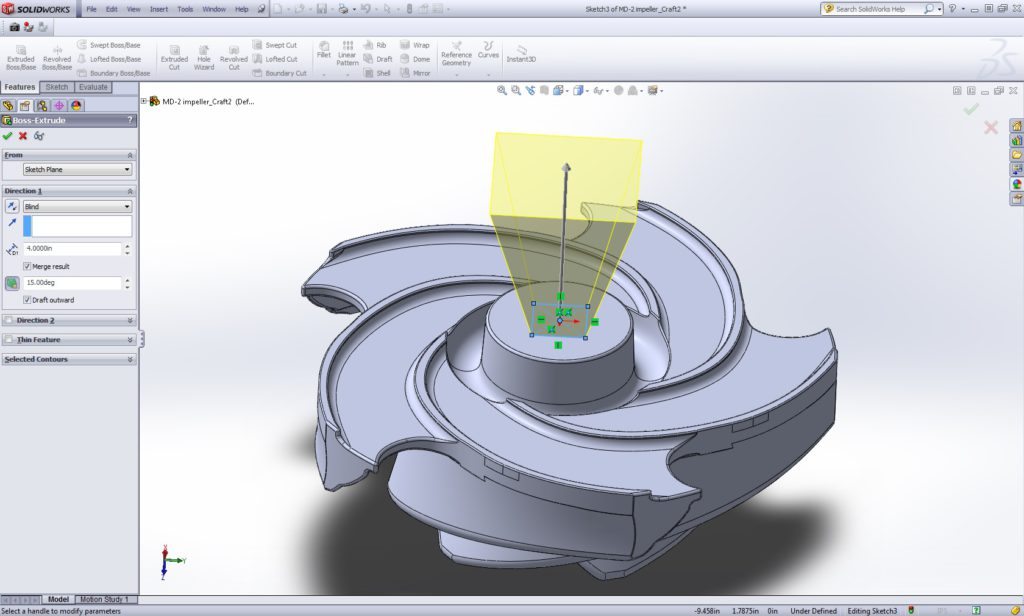
Using SolidWorks to Design a Casting
Care should be taken when designing castings so as not to inflate the cost of the part unnecessarily. Minimizing complex or non-value added features, incorporating minimally aggressive parting line conventions and allowing for adequate draft are key factors to success.
Cores add cost to both the tooling and casting processes and should be reserved for situations when their use offsets the cost of additional machining operations. Parting lines should be kept as flat, or planer, as possible. Drastic changes in parting orientation or direction should be avoided. These sharp transitions generate steep “shut-offs” in the mold, which can contribute to casting quality problems, excessive finishing costs and, in extreme cases, the addition of cores.
Draft needs to be present, but should not be excessive. The amount of draft relief over the length of a feature is more important than the draft angle itself. The number varies depending on equipment and process parameters. In general, .030″ to .060″ (.8 to 1.6 mm) of draft should be a good starting point for most foundries. However, in some situations the foundry will require more than this. (i.e. blind holes & pockets, tight corners, deep parting offsets, etc…)
If specifying a draft angle, be aware that small numbers can add up fast. A 10″ deep pocket with 3 degrees of draft will have over 1/2″ (12 mm) of draft material added. This not only adds significant weight to the casting, but could also affect the solidification behavior of the casting which could lead to defects.
There are also different types of, or ways to apply, draft. Traditional, radial and natural are all conventions used to streamline the tooling and casting process. Application of and when and where to use each method is a skill that takes time and practice to master.
Be aware of draft convention and consider the effects of “plus draft”, or added draft, versus “minus draft”. (“Plus draft” is usually considered the default unless otherwise specified.) Plus draft will hold the dimension at the furthest point from the parting line and add material. Minus draft will hold the dimension at the parting line and remove material from the casting. This is usually reserved for situations where clearance to mating parts is of concern.
Working with the foundry and pattern shop to address these issues on the front end of the casting design will go a long way toward making your casting design a success. Contact our team of skilled casting and CAD engineers to see how we can help you get your casting design started on the right foot!
The post When Designing Castings, Don’t Get Shut-Out by Shut-Offs…and Other Pitfalls to Avoid. appeared first on Craft Pattern & Mold Blog.